Non è certamente la prima volta che la famiglia Chizzoni di Bozzolo (Mn) compare sulle pagine di questa rivista. Lo fece, per esempio, nell’ottobre del 2021, quando descrivemmo nei dettagli la nuova sala rotativa – una delle prime installate in Italia – che andava a prendere il posto di una 14+14 a spina di pesce, ormai del tutto inadeguata a mungere gli oltre 600 capi che contava (allora) la mandria. Più recentemente, Roberto Chizzoni è stato premiato come Allevatore dell’anno 2023, per la categoria Bovini da latte.
Erano passati soltanto due anni e mezzo dal servizio precedente, ma nel frattempo la mandria era lievitata fino a 900 capi. Consistenza che mantiene ancora oggi, autunno 2024, ma che è destinata a mutare ulteriormente entro pochi mesi. Quando, ci dice Davide, figlio di Roberto, si dovrebbe raggiungere quota mille. «E lì ci fermeremo, essendo arrivati al nostro obiettivo. Contemporaneamente, dovrebbe concludersi l’ampliamento delle strutture dedicate a vitelle e rimonta, per dare maggior spazio e benessere anche agli animali giovani, oggi parzialmente ospitati in igloo all’aperto».
Crescita impressionante
È difficile credere che tutto ciò che vediamo oggi sia nato in poco più di 35 anni. L’azienda Canili, dove ci troviamo, fu infatti fondata da Roberto e dal padre Luigi nel 1988, acquistando stalla e un po’ di terreni adiacenti.
«A quei tempi – ci dice Davide – avevano 25 animali. Il numero attuale è stato raggiunto anno dopo anno, confidando sempre sulla rimonta interna, senza acquistare nulla fuori dall’azienda». Con una progressione, aggiungiamo noi, impressionante: 200 capi a inizio millennio, 400 nel 2020, 650 nel 2021 e mille, una più una meno, dal 2025 in poi: significa +150% nel giro di cinque anni scarsi.
Contemporaneamente si è lavorato sulle strutture, come già evidenziato, ma anche sulle dotazioni. Per esempio, con l’installazione della sala rotativa da 60 poste Streamline 360EX della Boumatic, che da un giorno all’altro ha dimezzato i tempi di mungitura. «Abbiamo iniziato la pratica per la nuova sala prima del Covid, ma l’epidemia ci ha bloccati. Nonostante ciò, la mandria ha continuato a crescere e la vecchia sala era diventata del tutto insufficiente. Quando ci trasferimmo nella nuova avevamo ormai 700 capi; per mungerli ci volevano otto ore. La rotativa, mungendo 250 capi ogni ora, ce la fa in meno di quattro ore».
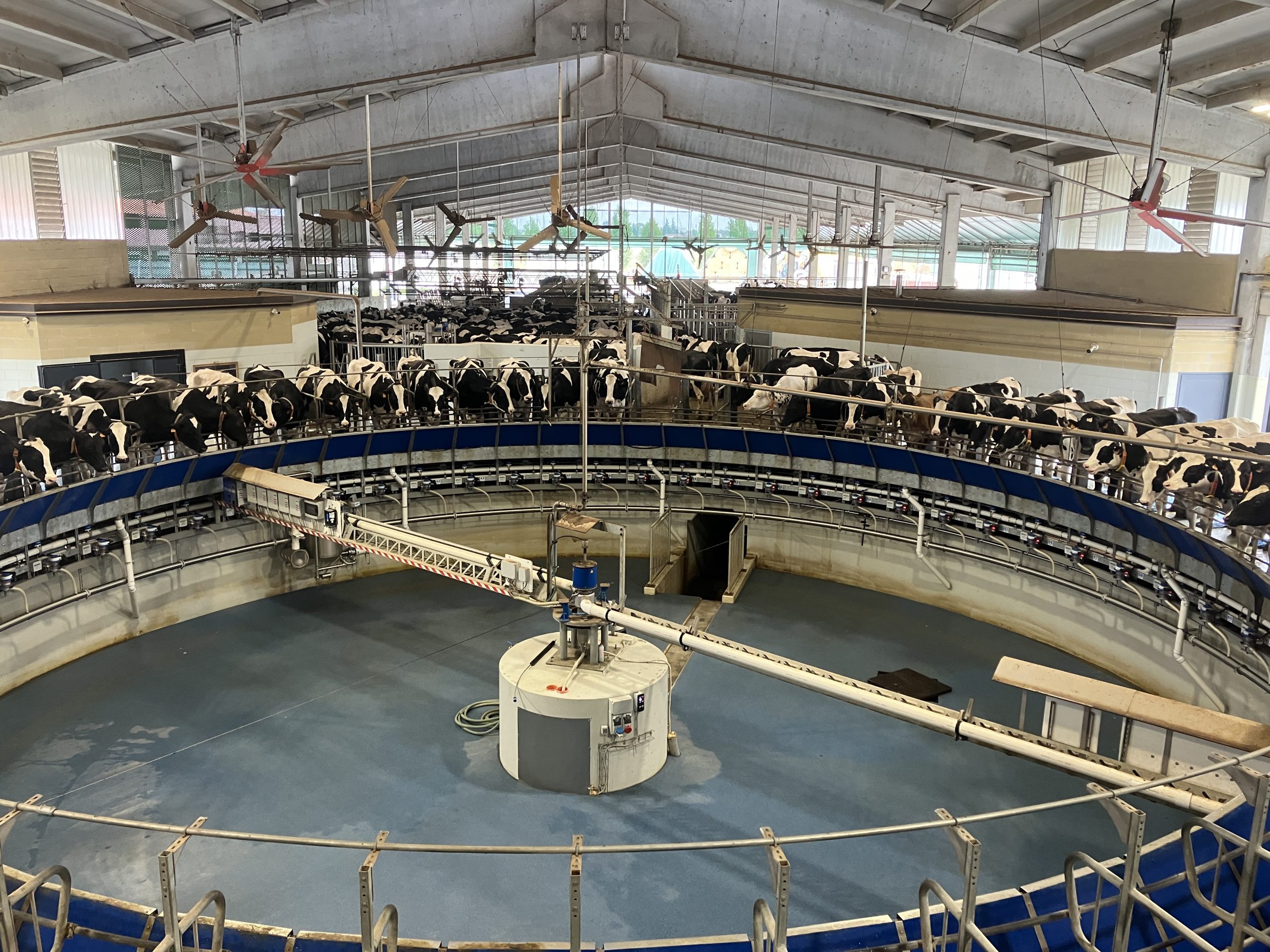
Stalla connessa
Al di là dell’innegabile necessità di aumentare (fortemente) la capacità di mungitura, la scelta di adottare una nuova sala fu fatta anche per dare un ulteriore impulso alla digitalizzazione dell’allevamento, per la verità già piuttosto avanzata.
«Iniziammo a usare gli attivometri quando avevamo circa 200 capi. Ai tempi, la forza lavoro era composta al 50% da noi della famiglia: oltre a mio padre e a me, sono infatti impegnati in azienda mia madre e mia sorella Chiara. Tuttavia, anche con quel numero di capi e quella suddivisione della manodopera, vedemmo un cambiamento significativo nel tasso di gravidanze. Non voglio pensare cosa accadrebbe oggi, con 900 vacche e 15 dipendenti, senza la tecnologia. In una stalla moderna è diventata imprescindibile. Per la salute, i calori, l’analisi della produzione, tutto quanto».
Le stalle da mille capi non sono comuni in Italia, sebbene la dimensione media delle aziende appaia in netta crescita. Non possiamo dunque fare a meno di chiedere al giovane allevatore se considera quello fatto dalla sua famiglia come un percorso obbligato per una realtà che voglia stare sul mercato.
«Non so se tutte le stalle dovranno superare i 500 capi o più. Quello che so con certezza è che per restare sul mercato bisogna investire. Mettere un po’ di capitali nell’azienda ogni anno, per restare al passo con i tempi. Non parlo soltanto di dimensioni. Pensiamo al benessere animale: le nostre strutture più vecchie hanno meno di 30 anni, tuttavia se non le avessimo adeguate di volta in volta, sarebbero obsolete. Mercato, normative, sensibilità dei consumatori: tutto cambia molto rapidamente e un’azienda che non investe per mantenersi al passo, nel giro di cinque anni accumulerebbe ritardi forse incolmabili».
Nutrire duemila capi al giorno
La zootecnia di precisione coinvolge anche, e non potrebbe essere altrimenti, la nutrizione degli animali, con ricette diversificate per i vari gruppi, impiego di alimenti di alta qualità e necessità di rispettare rigorosamente dosaggi e omogeneità dell’unifeed. «Praticamente tutti i foraggi che utilizziamo provengono dai nostri terreni o da un paio di agricoltori cui forniamo il digestato e che ci cedono un po’ di mais e frumento, in una sorta di economia circolare», spiega Davide Chizzoni.
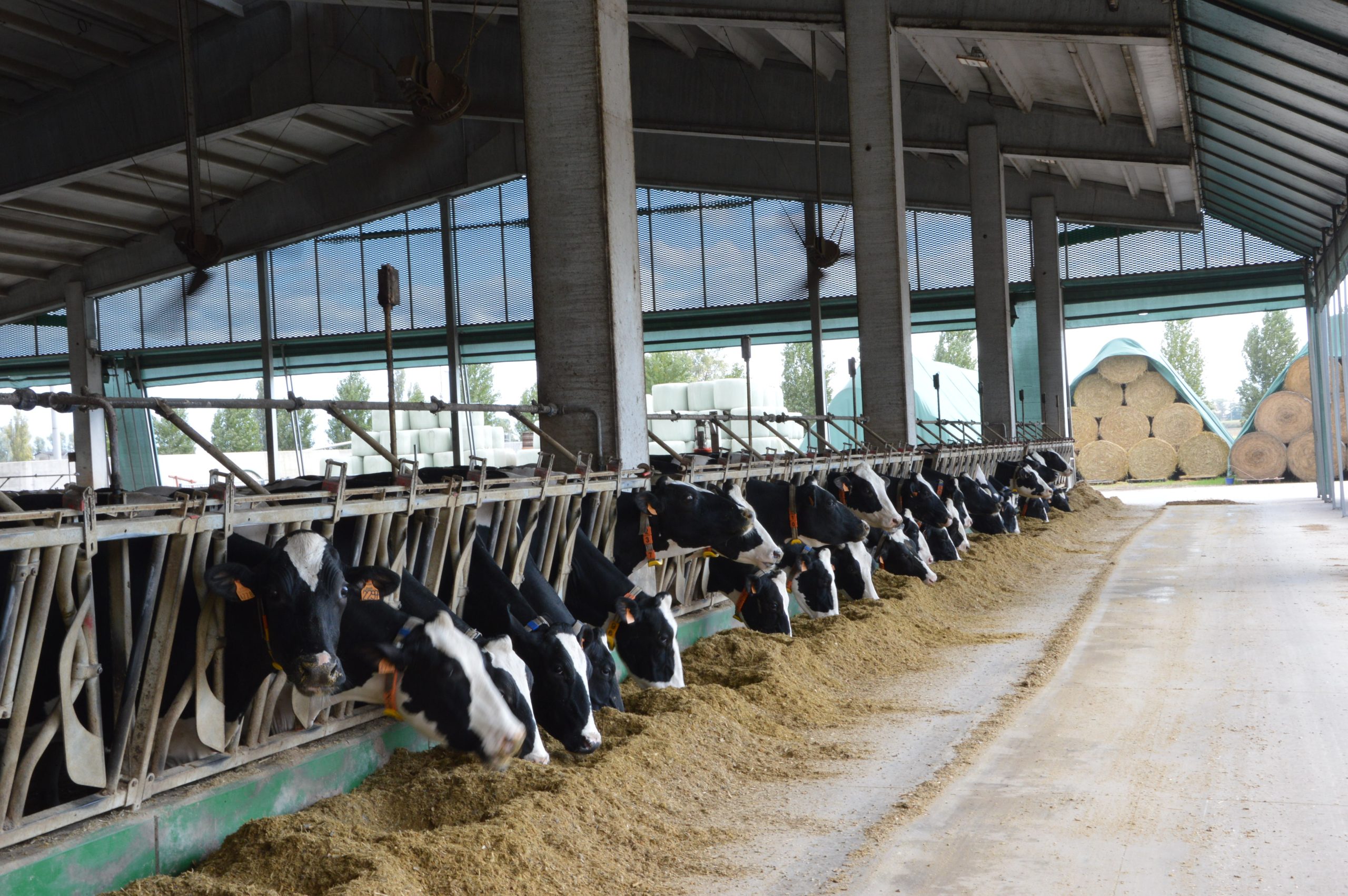
La razione, prosegue, è composta da silomais (17 kg circa), pastone integrale (9 kg), 7 kg di frumento insilato fresco, 6 kg di trebbie di birra, due chili di medica in balle fasciate e mezzo chilo di paglia, oltre ai vari concentrati. «Preparare l’unifeed correttamente non è semplice, sia perché esistono varie ricette per i diversi gruppi, sia perché si possono creare problemi di comunicazione e di trasmissione delle informazioni corrette. Per questo motivo abbiamo cercato di automatizzare il più possibile questa fase. Quando si è in tanti, standardizzare i processi è indispensabile».
Partnership con Sgariboldi
Un elemento fondamentale di questa automazione è il carro miscelatore, che all’azienda Canili è marchiato Sgariboldi. «È ormai il terzo che prendiamo e quest’ultimo in particolare è stato praticamente realizzato sulle nostre richieste. Diciamo che la Sgariboldi ce l’ha cucito addosso, come fosse un vestito. È uno dei pregi principali di quest’azienda, avere una grande capacità di ascolto verso le esigenze di noi allevatori. Se c’è un problema, per esempio un ingresso basso o che so io, adattano il carro, fabbricandolo quasi su misura. Credo che in questo modo si complichino la vita, per esempio per il magazzino dei ricambi, ma per i clienti è davvero un grosso vantaggio».
La partnership tra Sgariboldi e la famiglia Chizzoni iniziò nel 2007, con un Gulliver orizzontale. «Prima avevamo carri trainati di altri marchi, ma per il passaggio al semovente scegliemmo Sgariboldi e da allora non abbiamo più cambiato». Dieci anni dopo il Gulliver, arrivò il primo Grizzly, un 8130 a doppia coclea, ancora presente in azienda. «Quando nel 2023 abbiamo preso il nuovo Grizzly, un 8132/2 Titanium da 32 metri cubi, abbiamo tenuto anche il primo. Lo usiamo come muletto, ma anche per aiutare il nuovo carro nel lavoro. Con così tanti animali da nutrire, le ore si accumulano: in un anno e mezzo abbiamo superato le 4.500, nonostante si usi il vecchio Grizzly per alimentare la rimonta».
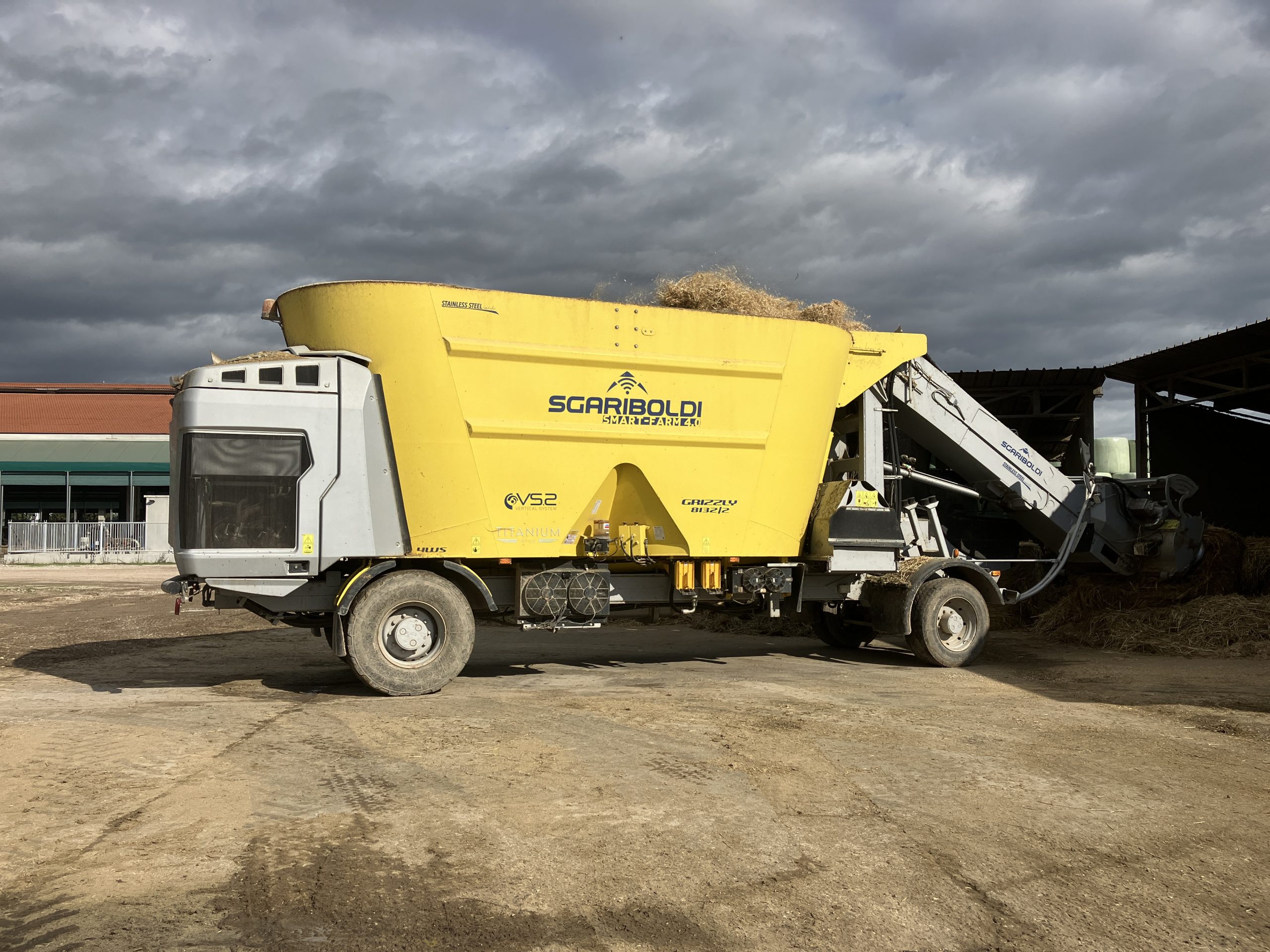
Le richieste di personalizzazione fatte sul primo modello, prosegue Chizzoni, «sono state realizzate senza nessuna obiezione e quando ci hanno consegnato il nuovo carro, abbiamo visto con piacere che gli stessi interventi erano già presenti. Aver trasformato i nostri suggerimenti in modifiche definitive dimostra attenzione per le informazioni che arrivano dalle stalle».
Mai più senza mulino
«Sia il vecchio Grizzly sia questo sono dotati di mulino. Per noi è irrinunciabile. Dal punto di vista della razione, introdurre ingredienti già tagliati ha il grosso vantaggio di rendere più veloce e omogenea la miscelazione. Per esempio, non si formano zolle di prodotto che non si mescolano con il resto perché hanno una lunghezza diversa. C’è poi un evidente beneficio economico: grazie al mulino l’operatore non scende mai dal carro, per cui non si hanno tempi morti e i consumi di gasolio, di conseguenza, scendono».
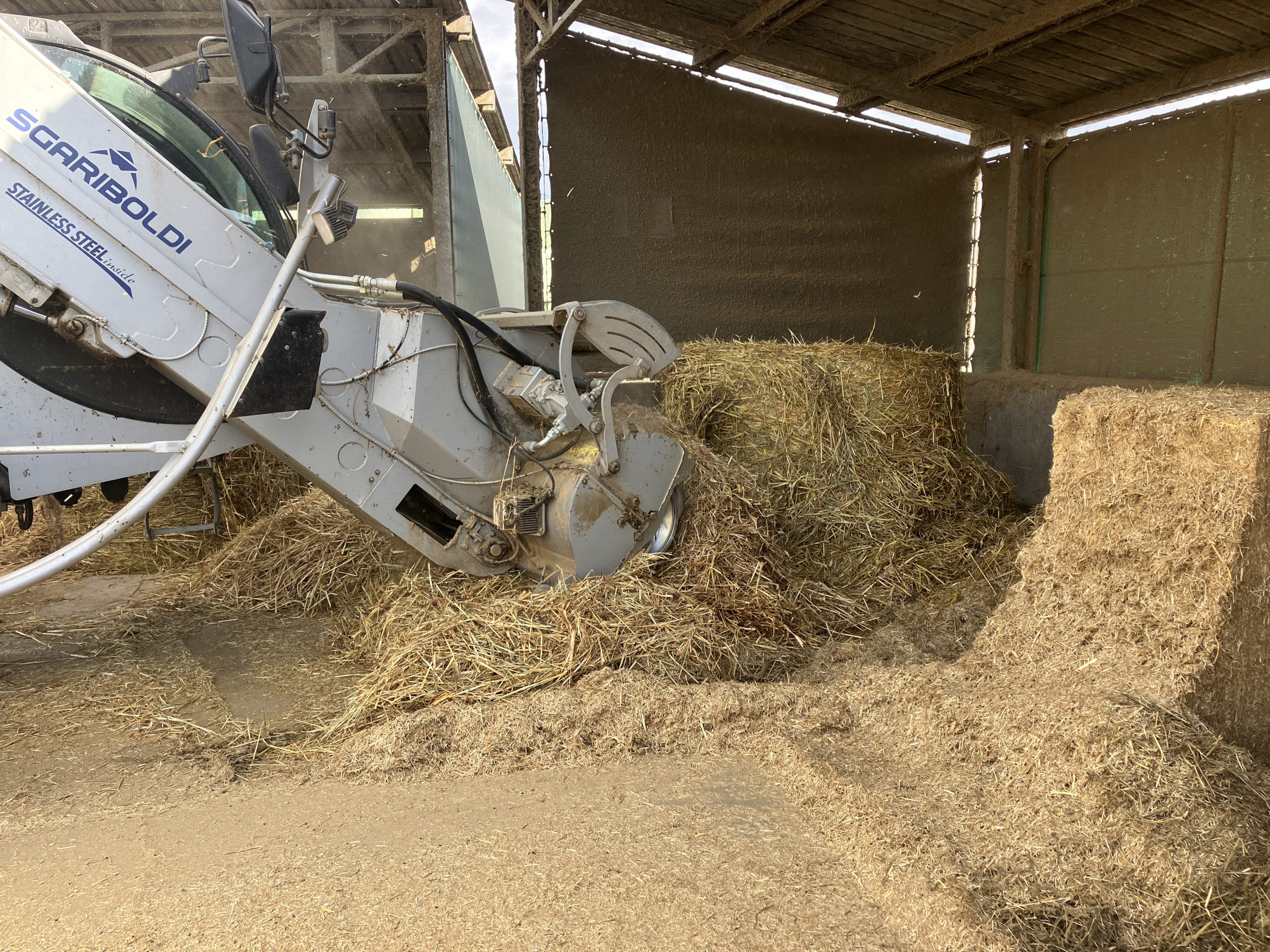
A ridurre i costi energetici, aggiunge Chizzoni, ha pensato anche la nuova conformazione del motore. «Il vecchio Grizzly – che poi tanto vecchio non è, ha sette anni – richiedeva in media 20-21 litri l’ora. Quello nuovo, pur avendo 25 cavalli in più, non va oltre i 17 litri per ora di funzionamento».
Infine, il mulino riduce la necessità di manutenzione alle coclee, in quanto i coltelli si usurano meno. Ne derivano tempi di intervento più rapidi e maggior semplicità di manutenzione.
Nessun rischio di errore
Oltre ad essere completamente in linea con Agricoltura 4.0, il Grizzly Titanium 8132/2 monta un rilevatore Nir di Dinamica Generale, grazie al quale sbagliare miscelata è praticamente impossibile. «Il sistema, installato dietro alla fresa, legge l’umidità del prodotto caricato e in base ai valori rilevati aumenta o riduce la quota di quell’ingrediente per adeguare l’effettiva sostanza secca a quanto previsto in ricetta. Tutte le nuove impostazioni, per esempio una variazione di qualche ingrediente, passano direttamente dal pc dell’ufficio al carro, mentre con il vecchio modello certe integrazioni richiedevano ancora la chiavetta. Discorso analogo per gli aggiornamenti software: arrivano direttamente dalla casa madre, senza che noi si faccia nulla».
Con la pesatura elettronica e il controllo digitale degli ingredienti, naturalmente, non vi sono possibilità di cattive interpretazioni. «In un’azienda con tanti dipendenti è un aspetto fondamentale. Finché la razione è preparata dal proprietario, il quale parla direttamente con l’alimentarista, passi. Ma se vi sono due o tre passaggi di consegne, il rischio di fraintendimenti sale esponenzialmente. Lo stesso vale per l’adeguamento del carico alle condizioni dei vari prodotti: quando si stima l’umidità a occhio, non si è mai precisi. Idem per i tempi di taglio e miscelazione. Ogni alimento ha i suoi e ogni operatore li interpreta secondo la sua esperienza. Con un carro ad alta tecnologia, fa tutto il computer e l’uomo è sollevato da ogni responsabilità. Deve soltanto guidare».
Miscelata perfetta
«Periodicamente controlliamo sia l’omogeneità della miscelata, sia quella della distribuzione e i setacci sono sempre perfetti. L’abbinamento tra l’azione del mulino e quella delle coclee fa sì che la razione sia ben miscelata e per le vacche diventi molto difficile selezionare gli alimenti».
La prova del nove, aggiunge il giovane allevatore, si ha quando qualcosa non funziona. «Ormai siamo talmente abituati a lavorare in un certo modo che fatichiamo a renderci conto di quale sia il livello raggiunto. Ce ne accorgiamo soltanto se qualcosa viene a mancare. Per esempio, tagliando solo con le coclee, senza il mulino, si nota immediatamente il cambio di performance della mandria. A noi sembra di aver fatto la stessa identica razione, ma gli animali dimostrano che non è così».
Alla luce di tutto questo, conclude Chizzoni, tornare indietro è impossibile. «Per un’azienda come la nostra è indispensabile un elevato standard di lavoro e non potremmo scendere a compromessi. Vale anche per il Grizzly. Qualità della miscelata, comodità d’uso, risparmio economico sono un valore aggiunto a cui non possiamo più rinunciare».
Dopo il benessere animale tocca alla sostenibilità
Con duemila capi, tanti ne conta, tra lattazione, asciutta e manze l’azienda Canili, i reflui possono diventare un serio problema. La famiglia Chizzoni l’ha risolto trasformandolo in opportunità. Ha infatti realizzato, meno di un anno fa, un digestore da 300 kW, che si affianca a un impianto fotovoltaico da 70 kWh, in fase di ampliamento per rendere l’azienda autosufficiente dal punto di vista energetico.
«Con il biogas produciamo energia elettrica che immettiamo nella rete e acqua calda per tutti gli usi dell’azienda. In più abbiamo il digestato, che rappresenta una risorsa economica e anche ambientale», commenta Davide Chizzoni.
Inizialmente scettico sull’ipotesi di dedicarsi alle agroenergie, l’allevatore ammette di aver dovuto cambiare idea. «Mi sono reso conto che la sostenibilità degli allevamenti è il tema del futuro. Il benessere animale è ormai arrivato a livelli tali da necessitare soltanto piccole correzioni, mentre sul fronte ambientale c’è ancora molto da fare e soprattutto da comunicare. Gran parte della nostra attività è già green, ma l’opinione pubblica non lo sa e una miglior gestione dei reflui, resa possibile dalla digestione anaerobica, ci aiuta a dimostrarlo».
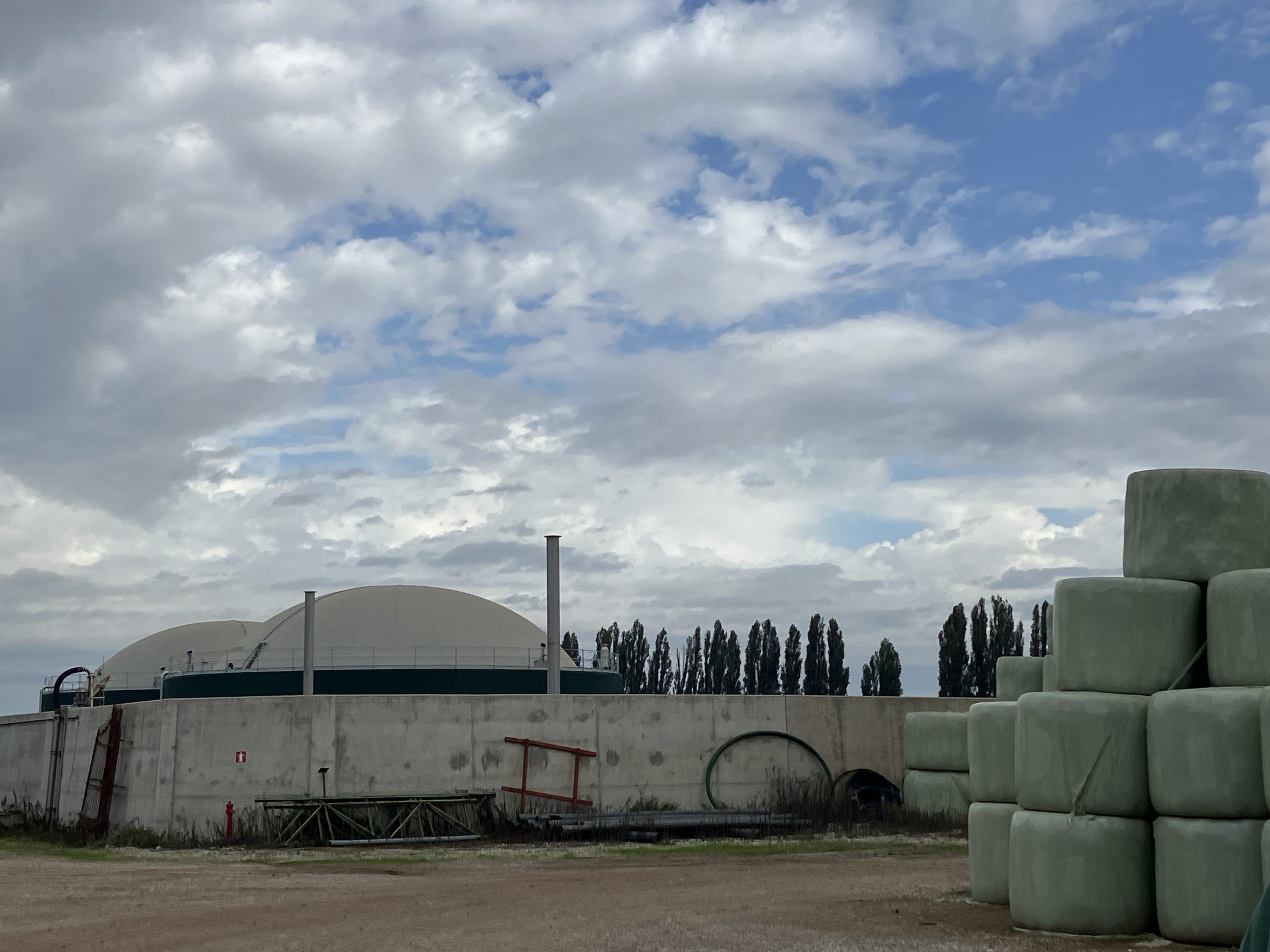
Un orso duro come il titanio
Titanium è la versione ad alta capacità della gamma Grizzly; un allestimento costruito con acciai speciali e pensato per i grandi allevamenti, che necessitano di caricare grandi quantitativi di materiale. È proposto in diverse cubature: da 30 a 40 mc nella versione standard, con due assi e due coclee, e ora anche in versione XL a tre assi e tre coclee, con volume fino a 45 mc.
Entrambe le versioni sono equipaggiate con sistemi 4WS (per Titanium standard) e 6WS (per Titanium XL), per la massima maneggevolezza. La quale è in effetti elogiata da Davide Chizzoni come uno dei pregi principali del carro, accanto alla qualità della miscelazione e alla possibilità di gestire l’intero processo di preparazione dell’unifeed senza mai uscire dalla cabina.
Generalmente motorizzato con un 6 cilindri John Deere con potenza fino a 300 cavalli, il Grizzly Titanium 8132/2 ha una lunghezza complessiva di 11,2 metri, una massa di 146 quintali e velocità massima fino a 40 km orari.
Tra le caratteristiche principali del modello in uso a Cascina Canili ricordiamo la fresa da 2,2 metri, la cabina intelligente I-Cab di seconda generazione, ampliata e aggiornata rispetto alla versione precedente, con bracciolo integrato nel sedile, joystick interattivo e display da 12 pollici. Infine Intellitechnology, una sofisticata tecnologia di bordo che comprende, oltre a I-Cab II, anche Intelliloader, un sistema di carico intelligente dotato di programmazioni predefinite per il taglio dei diversi alimenti e sistema Intellimixer, in grado di regolare automaticamente i giri delle coclee.
LEGGI L'ARTICOLO PUBBLICATO SU IZ 19.2024